Researchers from the School of Mechanical Engineering at Purdue University have developed an innovative new patterning approach for applications like drug delivery in biomedical applications. Detailing their research in the recently published ‘3D-Printed Microrobots with Integrated Structural Color for Identification and Tracking,’ the authors give us insight into new patterns on the micro- and nanoscale using two-photon polymerization (TPP), a technique that offers submicron resolution.
While microrobots (divided into biological, hybrid, and synthetic groups) are helpful in applications like micromanipulation and advanced sensing, there are still obstacles in development of miniature structures because of the need to combine actuation and wireless control within one device. Size is the issue in many cases, although actuation is often provided externally. There are also extensive challenges for in vitro and in vivo processes with the use of microrobotic systems, visuals, and tracking.
“For 3D printed microrobots with smaller dimensions, alternative fabrication approaches are needed to integrate distinctive tracking features, including marking the microrobot surfaces with fluorescent materials such as quantum dots or using fluorophores selectively attached to specific functional groups,” stated the researchers. “Despite their success in tracking, these materials lose their fluorescence over time, limiting their duration of usefulness.”
In this study, color plays a large role, with patterns comprised of prism arrays pointing upward—permitting the team to integrate them onto different areas of the microrobot. Patterns were developed as follows:
- Red pattern – blocks with a 160 nm x 170 nm footprint
- Green pattern – blocks with a footprint of 120 nm x 90 nm
- Arrays on both of the helix and platform microrobots consist of all red (R), all green (G), or alternating red and green (RG) blocks

Fabrication and characterization of 3D-printed microrobots with structural colored features. A) Fabrication process of the 3D-printed microrobots: (i)–(iii) IP-DIP photoresist is deposited on a glass slide and the microrobots are printed using a TPP fabrication system (Nanoscribe Photonic Professional GT); (iv) removal of nonpolymerized photoresist; (v)–(vi) Ni and Ge are sequentially deposited (100 and 35 nm, respectively) onto the structures at 2 Å sx1 ; (vii) microrobots are moved to an aqueous solution and later released using a micropipette. B) (i) CAD design of helical microrobots with a structural colored area located on the top surface of the helix head. Different unit cell designs include, G, and RG, based on dimensions from Nagasaki et al.[41]. (ii) Scanning electron microscope (SEM) image of a single helical microrobot with 10 x RG pattern and (iii) optical image of the same structure under white light expressing color. C) (i) CAD image of control platform microrobot design with a structural color pattern. (ii) SEM image of the control platform with 5 x RG pattern and (iii) optical image of the same structure under white light expressing color. (Note: saturation value during the optical image acquisition: 4, according to Basler’s Pylon Viewer software).

Structural color characterization. A) Expressed color from the helical microrobots plotted in the CIE1931 color space using RGB values obtained by ImageJ. Optical image of the expressed color versus angle by the helical-like microrobots: B) 5 x R, C) 5 x G, D) 5 x RG, and E) 10 x RG.
“The RG pattern was shown to express a wider spectrum of colors in comparison to just R and the G patterns alone,” stated the researchers. “The R and G patterns expressed bright colors of blue and red only, whereas RG additionally expressed bright green.
“Fine tuning of color expression depending on the applied angle can potentially provide real-time information of a microrobot’s position in both x–y and z directions by identifying the change in color while it is moving in the 3D workspace.”
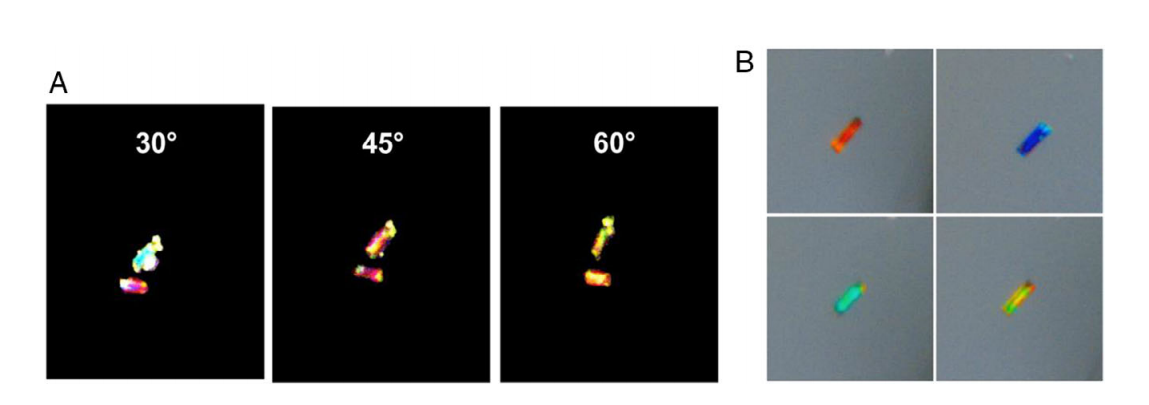
Structural color with respect to vertical tilt. A) Released control platforms on a planarized silicon wafer tilted at 30, 45, and 60 out of the horizontal plane. (Note: the image background has been removed for clarity.) B) Control platforms with one edge fixed to a transparent substrate and the other tilted out of plane at different amounts using magnetic fields resulting in different color expressions. For both parts (A) and (B), the lamp was held in the same position while the platforms were tilted.
Helical microswimmers relied on rotating magnetic fields for actuators, while the control platform microrobots used gradient fields relying on the MagnebotiX coil system. The researchers noted that as the control platforms rotated, color was visible, as well as on the helical robots using low frequencies. The researchers did note though that color differed depending on orientation and light source.
“The variation of structural color block dimensions was used to explore the ability to manipulate color expression. In this study, the alternating block geometries provided a wider range of colors than arrays with a single type of block geometry,” concluded the researchers. “With increasing accuracy of micro-3D-printing technologies and by exploring complex patterns, noniridescent colors can be obtained.
“This has been recently demonstrated for 3D printed lamellar-like structures similar to the ones of the Morpho butterfly, though this type of pattern only expressed an artificial blue color and was not applied to structures while moving. By exploring new computationally designed structures and integrating them into 3D microrobotic systems, structural color can become a common element not only for tracking and identification but also for creating tunable surface properties.”

Color tracking and motion evaluation. Optical images of A) a helical microrobot with integrated structural color on its head, expressing a red, next to a control microrobot with no nanopatterns integrated on its head; B) color expressed at (i) low and (ii) high frequencies; C) two colored helical microrobots with different nanopatterns on a transparent substrate. D) Color-based tracking algorithm applied to a colored helical microrobot, where the real optical image (i) is recognized by the algorithm with the color-tracking mask shown in image (ii). E) Compilation of the microrobot tracking, with a starting position indicated by ti and its ending position as tf. Scale bar, 50 μm.
Microrobotics and drug delivery systems continue to be impacted by 3D printing in research projects involving innovative microstructures, spermbots, and a variety of different techniques. What do you think of this news? Let us know your thoughts! Join the discussion of this and other 3D printing topics at 3DPrintBoard.com.
[Source / Images: ‘3D-Printed Microrobots with Integrated Structural Color for Identification and Tracking’]Subscribe to Our Email Newsletter
Stay up-to-date on all the latest news from the 3D printing industry and receive information and offers from third party vendors.
Print Services
Upload your 3D Models and get them printed quickly and efficiently.
You May Also Like
The Business Case for Binder Jet in an Uncertain World: Changes, Part 4
In rough seas, binder jet as a market is underpinned by a collection of firms, some large and small. We looked at their potential staying power, the applications and parts,...
The Business Case for Binder Jet in an Uncertain World: Shook Ones, Part 3
In the classic tune Shook Ones Pt II by Mobb Deep, we get introduced to “all of those who wanna profile and pose,” but when the going gets tough, they...
The Business Case for Binder Jet in an Uncertain World: On A Jet Plane, Part 2
We’re in the doldrums. And binder jet is more in the doldrums still. In the first article in this series, we looked at how Jedi Mind Tricks got us to...
The Business Case for Binder Jet in an Uncertain World: Jedi Mind Tricks, Part I
You’ve probably noticed that the binder jet market has been rather rocky as of late. Voxeljet was delisted, was not sold, and is now restructuring. Nano Dimension subsidiary Desktop Metal...